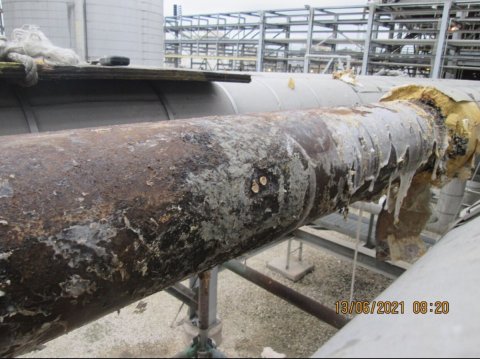
Utrata szczelności to jedna z głównych przyczyn wystąpienia awarii. Zbiorniki, rurociągi w trakcie ich eksploatacji poddane są działaniu różnych mediów, rzecz jasna wywołujących narażenie ich powierzchni na niszczenie korozyjne, przyspieszone wycieranie. Konieczność interwencji serwisowej, dokonania kosztownej wymiany, zatrzymania ruchu (produkcji), ryzyko wypadku dla pracowników, a nawet katastrofy obiektu technicznego to konsekwencje stałego zużywania się materiałów prowadzące do wystąpienia niekontrolowanego lub niespodziewanego wycieku. W jaki sposób zapobiec awarii i jak dokonać wzmocnienia osłabionych elementów instalacji?
Korozja rozumiana jako niszczenie materiałów, zwykle metali, jest wynikiem oddziaływania tych materiałów z środowiskiem. Zatem, aby zapobiec niszczeniu materiałów konieczne jest odpowiednie zabezpieczenie ich powierzchni przed agresją środowiska. Oczywiście dostępne są bardzo różne sposoby ochrony przeciwkorozyjnej, w tym najczęściej stosowana (80% wszystkich działań) ochrona powłokowa. Stosuje się także ochronę elektrochemiczną oraz rzadziej modyfikację środowiska (inhibitory, klimatyzacja, osuszanie itp.). Podstawową kwestią w kontekście trwałości obiektu chronionego, jest odpowiedź na pytanie – czy zastosowana ochrona powłokowa (lub inna) jest dobrze zaprojektowana dla ekspozycji obiektu w danym środowisku? tzn. na jaki okres trwałości zabezpieczenia możemy liczyć lub jaki jest spodziewany czas eksploatacji bezawaryjnej. Koniecznym staje się zatem nie tylko określenie doraźnej odporności zabezpieczenia na oddziaływanie ze środowiskiem (np. stal/powłoka/kwas), lecz należy także uwzględnić barierowość powłoki, czyli „szczelności materiału powłoki” na przenikanie skrośne czynników korozyjnych (woda, chlorki i inne jony). Wykonanie zabezpieczenia powłokowego, mimo że w początkowym okresie daje nam komfort „świętego spokoju”, to jednak wraz z upływem czasu bez naszej świadomości może dochodzić do stopniowego lub nagłego pogorszenia ochrony. Oczywiście zdarza się to w przypadku złego doboru powłok, ale też z powodu niestabilnego środowiska pracy obiektu (zmienne stężenia zanieczyszczeń, zmienna temperatura – szoki termiczne) wykraczające poza możliwości i osiągi zabezpieczenia. Jeśli nawet postanowimy zrezygnować z powłok i np. zastosować stal nierdzewną (austenityczną, ferrytyczno-austenityczną znaną jako typu duplex), to i tak pojawi się problem korozji punktowej (wżerowej), na którą te stale są wrażliwe, a ewentualne podniesienie odporności stali (podniesienie stanu pasywnego – wzrost wartości współczynnika PREN) na korozję wżerową może okazać się nieopłacalne. Opisany obraz sytuacji wskazuje na nieuchronność procesów korozyjnych, które przebiegają w sposób ciągły, a których głównym efektem jest skrócenie czasu eksploatacji obiektu lub nawet wystąpienie nagłego uszkodzenia korozyjnego prowadzącego do awarii. Dobrym przykładem jest korozja stali (zbiorniki, rurociągi, kolumny) pod izolacją termiczną gdzie powierzchni stali zakryta warstwą wełny izolacyjnej, jest niewidoczna dla służb użytkujących obiekt i dopiero wyciek sygnalizuje, że jest problem (fot. 1). W innym przykładzie, gdzie nie spodziewano się problemu, korozja wywołała znaczne zmniejszenie grubości blachy stalowej, tym razem naprężenia własne pochodzące od spawania doprowadziły do przyspieszonej korozji w strefie spoiny (fot. 2).
Jak osiągnąć planowaną trwałość i uniknąć awarii?
- Odpowiedź jest prosta – zastosować odporny na warunki eksploatacji materiał lub odpowiednie zabezpieczenie przeciwko zużywaniu się stali (ogólnie materiałów) w następujących narażeniach:
- Przeciw wycieraniu
- Przeciw agresji chemicznej
- Przeciw korozji ogólnej i specyficznej (wżerowa, stężeniowa, naprężeniowa itp.)
Wśród powłok kompozytowych Belzona znajdziemy odpowiednio wytrzymały materiał dla zapewnienia niezawodnej eksploatacji obiektu poddanego narażeniem środowiska opisanego w punktach 1-3. W niniejszym opracowaniu skupiono się wyłącznie na przypadkach rozwiązania problemu gdy metal (lub inne materiały) uległ już zniszczeniu lub osłabieniu w wyniku jego eksploatacji niezależnie od tego czy był w jakikolwiek sposób zabezpieczony czy też nie posiadał żadnej ochrony.
Jeśli obiekt jest już w eksploatacji i dodatkowo wiemy o pogarszającym się stanie technicznym eksploatowanych elementów, to możemy zapobiec awarii poprzez odpowiednie wzmocnienie konstrukcji przeprowadzone nawet bez jej odstawienia z ruchu. Zadanie jest trochę ułatwione w eksploatacji zbiorników i rurociągów podlegających dozorowi technicznemu, głównie dlatego, że mamy tu obowiązek monitorowania stanu technicznego. Cykliczne przeglądy w tym np. pomiar grubości ścianki, pozwala na wcześniejszą reakcję w razie stwierdzenia mniejszych wartości w stosunku do nominalnych grubości. W skrajnym przypadku zmierzona grubość ścianki może być niższa od tzw. krytycznej lub dopuszczalnej grubości minimalnej. W takich przypadkach obiekt jest wyłączany z eksploatacji. Zbiornik stalowy przedstawiony na zdjęciu (fot. 2) – to właśnie taki przypadek, gdzie optycznie wygląda on dobrze natomiast pomiary ultradźwiękowe płaszcza stalowego wykazały obecność miejsc o krytycznych grubościach ścianki. Charakterystyczne okazało się to, że powodem utraty grubości była oczywiście korozja, ale rozwijająca się prawie wyłącznie w obrębie spoin spawalniczych. Szczegółowy rozkład zmierzonych grubości ilustruje rys.1.
Rys.1. Pomiary ultradźwiękowe grubości płaszcza stalowego zbiornika cieczy procesowej. Na zielono grubości nominalne
Czynnikiem przyspieszającym rozwój korozji okazały się naprężenia własne po spawaniu oraz lokalna zmiana struktury stali pod wpływem temperatury powstałej podczas spawania. Połączone oddziaływanie warunków środowiskowych (chlorki, wilgoć, inne zanieczyszczenia jonowe) oraz naprężeń, zarówno własnych jak i przyłożonych, wywołuje przyspieszenie procesów korozyjnych. W takim stanie omawiany zbiornik nie mógł już być eksploatowany. Rozważano dwa warianty naprawy sytuacji: spawanie nakładek z blachy stalowej w miejscach zniszczeń korozyjnych oraz budowa nowego zbiornika. W pierwszym przypadku naprawa jest skuteczna, ale nadal mamy do czynienia ze spoinami spawalniczymi i co więcej, tworzy się w tej technice dodatkowe obszary intensywnej korozji na skutek zwiększenia ilości połączeń spawanych. Oczywiście budowa nowego zbiornika na dotychczasowym projekcie jest rozwiązaniem problemu, ale bardzo kosztownym i wciąż pozostaje kwestia korozji płaszcza opisanej powyżej. W konkretnym przypadku zdecydowano jednak o zastosowaniu innowacyjnej techniki wzmocnienia zbiornika. Najbardziej osłabione korozją obszary płaszcza stalowego wzmocniono techniką kompozytową Belzona SuperWrapII. Technologia polega na wypełnieniu powstałych ubytków korozyjnych kompozytem polimerowym Belzona 1111 (fot. 3), tak aby wyrównać powierzchnię ścianki do grubości nominalnej, a następnie nakłada się warstwy specjalnej tkaniny z włókna węglowego (fot. 4) na specjalnej żywicy polimerowej (fot. 5 i fot. 6). Całość technologii naprawy zbiornika została uzgodniona z dozorem technicznym, a na wydanie zgody na przeprowadzenie naprawy istotny wpływ miały obliczenia przeprowadzone w oparciu o normę PN-EN-ISO 24817 oraz referencje z wcześniej przeprowadzonych napraw. Algorytm postępowania zawarty w normie, oparty na pełnych informacjach o parametrach eksploatacyjnych (ciśnienie w zbiorniku, temperatura, parametry otoczenia itp.), zaistniałych defektach, jak i po naprawie spodziewanym okresie trwałości obiektu, dokładnie określa sposób obliczenia wymaganej wytrzymałości oraz trwałości wzmocnienia. Dla opisanego przypadku zbiornika stalowego dokonano stosownych obliczeń i wyznaczono obszary do wzmocnienia systemem Belzona SuperWrapII.
Zasadniczo w normie PN-EN-ISO 24817 wyróżnia się dwie główne ścieżki obliczeń tj. jedna, gdy stwierdza się tylko zmniejszenie nominalnej grubości ścianki (wg normy typ defektu: A), natomiast drugi tok obliczeń jest dla przypadku wystąpienia perforacji ścianki (po prostu dziura, wg normy typ defektu: B). W omawianym przypadku perforacji płaszcza stalowego nie stwierdzono. W tabeli nr 1 podano parametry eksploatacyjne zbiornika oraz wyniki obliczeń technicznych systemu kompozytowego Belzona SuperWrapII jako wzmocnienia zbiornika.
Zbiornik stalowy cylindryczne o osi pionowej V2000 | |
Średnica (mm)
|
17750 |
Wysokość(mm)
|
10879 |
Ciśnienie obliczeniowe (bar)
|
0,025/-0,005 |
Temperatura robocza(oC)
|
-20 / +27 |
Masa aparatu pustego(kg)
|
74590 |
tdesign grubość warstwy kompozytu wzmacniającego (mm)
|
4 |
Ilość warstw tkaniny węglowej
|
2 |
Ilość warstw kompozytu Belzona®1982
|
4 |
Lover długość nakładki poza linią defektu (mm)
|
674 |