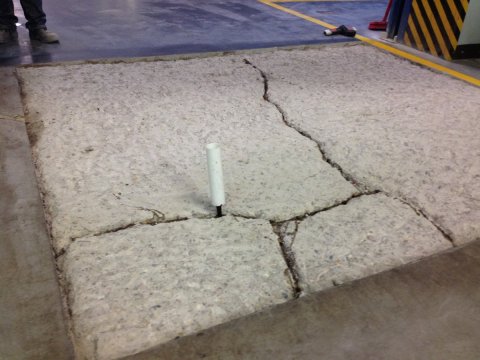
Podłogi przemysłowe poddane są różnego rodzaju obciążeniom. Wytrzymałość podłogi na obciążenia jest ściśle związana z jego rodzajem oraz może ono mieć charakter czysto mechaniczny, fizyko-chemiczny czy też wprost chemiczny.
Mechaniczne oddziaływanie na podłogę może mieć charakter skupiony lub powierzchniowy pochodzący od ciężkich maszyn-które mogą także znacząco obciążać podłoże dynamicznie - składowanych towarów i przemieszczających się obiektów, pojazdów czy ruchu pieszych. Każda podłoga przemysłowa składa się z odrębnie zaprojektowanych, lecz ściśle ze sobą współpracujących warstw: gruntu, podbudowy, warstwy poślizgowej i płyty betonowej z odpowiednio dobraną warstwą eksploatacyjną (WW warstwa wierzchnia). Każda z wcześniej wymienionych warstw musi spełniać konkretne zadanie a także wywiera wpływ na pozostałe warstwy (np. płyta nośna musi przenosić duże obciążenia stałe i dynamiczne). Jednakże, jeśli rozpatrujemy wytrzymałość podłogi na agresję chemiczną, to kluczowe znaczenie ma warstwa wierzchnia, potocznie zwana posadzką.
Poniższe opracowanie ma na celu przedstawienie kilku sposobów wykonania trwałych, szczelnych powierzchni podłóg przemysłowych. Jednym z szczególnych rodzajów obciążeń płyty betonowej są naprężenia własne betonu. Powstają one na skurczu jaki występuje podczas utwardzania betonu (hydratacji). Skurcz ten, jest traktowany w zasadzie jako odkształcenie betonu powstające pod wpływem naprężeń wewnętrznych i narastające w czasie bez udziału obciążeń zewnętrznych oraz bez zmiany temperatury. Proces ten jest długotrwały m.in. z powodu długiego wysychania-utraty wody z wnętrza betonu. Przy typowych grubościach konstrukcji betonowych zjawisko skurczu może być obecne w betonie nawet 3 lata! Rozróżnia się dwa rodzaje skurczu: powodowany wysychaniem (skurcz fizyczny) oraz skurcz autogeniczny (samoczynny, plastyczny). Skurcz autogeniczny spowodowany jest utratą wody, która wchodzi w reakcję z cementem (skurcz chemiczny) oraz wyparowaniem wody z zewnętrznych warstw zaczynu. Skurcz betonu może mieć charakter równomierny lub nierównomierny. Nierównomierny powstaje w wyniku bardziej intensywnego wysychania górnej powierzchni płyty betonowej w stosunku do wysychania jej wnętrza co prowadzi często do podnoszenia się narożników a co za tym idzie - wyginania płyty. Zjawisko to jest pierwotną przyczyną wielu uszkodzeń posadzki, zwłaszcza w narożnikach płyty betonowej, gdzie dochodzi do wyłamań lub uszkodzeń (fot.1. i fot .2). Skurcz równomierny jest z kolei powodem skracania się płyty posadzki. Prowadzi to w konsekwencji do zwiększenia się szerokości szczelin dylatacyjnych. W tym miejscu trzeba zwrócić uwagę na fakt, że szczeliny dylatacyjne są ciągle „żywe” nie tylko z powodu skurczu, ale i obciążeń zewnętrznych oraz wpływu temperatury. Wymagają one bardzo dobrych materiałów wypełniających w celu zapewnienia szczelności. Co za tym idzie, materiał do wypełnień powinien być bardzo elastyczny a także posiadać bardzo dobrą przyczepność do powierzchni krawędzi szczeliny dylatacyjnej. Spośród dużej ilości mas stosowanych w budownictwie warto zwrócić uwagę na elastyczny kompozyt polimerowy (wydłużalność 260%!) BELZONA®4511 (fot. 3). Produkt ten osiąga przyczepność do betonu, stali czy aluminium na tak wysokim poziomie, że podczas próby odrywania, uszkodzenie powstaje wewnątrz elastomeru a nie na styku z powierzchnią!
Zmienność odziaływań, które zachodzą na podłogi przemysłowe (skurcz, temperatura, obciążenia dynamiczne) powoduje, że strukturze betonu (w tym w płycie betonowej) powstają zarysowania lub niewidoczne spękania. Pęknięcia oraz mikropęknięcia (rysy) poddane ciągłym obciążeniom rozwijają się w strukturze betonu (propagują) łączą się tworząc swego rodzaju sieć, część z nich w końcu ukazuje się na powierzchni płyty co można zaobserwować jako bardzo charakterystyczną dla posadzek strukturę spękań nieregularnych, z pozoru bezładnych określanych również jako spękania klastrowe, a zgodnie z zasadami samoorganizacji powstała struktura wykazuje charakter fraktalny. Finalnym skutkiem propagacji zarysowań, mikropęknięć w betonie jest powstanie bardzo niekorzystnych wręcz uniemożliwiających dalszą eksploatację podłogi tzw. Makro-pęknięć dobrze widocznych „gołym okiem” (fot. 4 i fot. 5)
Podłogi przemysłowe są projektowane tak, aby beton użyty do ich budowy był materiałem sprężystym, a oddziaływania zewnętrzne (obciążenie mechaniczne, temperatura, środowisko), jak i wewnętrzne nie wywołały naprężeń przekraczających wytrzymałość na jego rozciąganie i nie wywołały zarysowania w przekroju. Niestety, w praktyce do zarysowań dochodzi bardzo często. Wówczas beton nie przenosi naprężeń rozciągających i w tym kierunku obciążenia przestaje być materiałem sprężystym. Bardzo często jest tak, że w trakcie użytkowania podłogi wykracza się poza czynniki ustalone na etapie projektowania np. incydentalne wprowadzenie pojazdów ciężkich lub gwałtowne manewry pojazdów kołowych, które przeciążają powierzchnię podłogi. Z tego powodu stan odkształceń i naprężeń może przekroczyć te dopuszczalne, co jest bezpośrednią przyczyną powstania spękań i innych uszkodzeń struktury betonu. Obciążenia dynamiczne podłogi wywoływane przejazdami pojazdów kołowych (wózki widłowe itp.) mogą chwilowo osiągać bardzo wysokie wartości nacisku, zwłaszcza w strefie jej warstwy wierzchniej płyty betonowej. Pojazdy wywołują nacisk, który co do wartości jest równy ciśnieniu jakie występuje w oponie pojazdu (max. 1MPa) natomiast w przypadku opon pełnych, naciski przyjmują znacznie większą wartość - średnio na poziomie 4MPa. Choć oba typy opon przenoszą takie same obciążenia, to jednak ze względu na różne powierzchnie styku opony z płytą podłogi wywołują zupełnie różne naciski na jej powierzchnię! Im bardziej wykonanie kół jest specjalne np. z tworzyw, takich jak PU (poliuretan) PP itp. tym wyższe naciski na powierzchnię i w przypadku wymienionych materiałów osiągają one wartość do 7MPa a zdarza się nawet nacisk na poziomie 20MPa!
W takim przypadku należy wzmocnić warstwę wierzchnią podłogi, w tym naroża szczelin dylatacyjnych. Rozwiązanie tej kwestii może zapewnić warstwa kompozytowa BELZONA®4111 Magma Quartz, która znacząco zwiększa wytrzymałość powierzchni posadzki tj. do poziomu ponad 100 MPa. Taka wytrzymałość pozwala nawet na bezpieczne przejazdy pojazdów z małymi kołami stalowymi (paleciaki, wózki samojezdne AGV itp.). Warstwa kompozytowa BELZONA®4111 jest także odporna na wycieranie a dzięki wysokiej przyczepności do podłoża betonowego zapewnia stabilną pracę podłogi oraz właściwy transfer sił wywołanych obciążeniem zewnętrznym i odkształceniami płyty. Biorąc pod uwagę strukturę obciążeń, zmienność warunków środowiskowych oraz innych możliwych oddziaływań na powierzchnię w części opisanych w tym opracowaniu, to widać, że podłogi przemysłowe możemy zakwalifikować do najbardziej narażonych na uszkodzenia obiektów budownictwa przemysłowego. Jeśli np. podłoga zaprojektowana jest z uwzględnieniem wszystkich możliwych obciążeń statycznych jest w stanie bezpiecznie (bez ryzyka uszkodzenia) przenosić wymienione obciążenia to już z pozoru drobna zmiana layout ‘u lub postawienie ściany w innym miejscu może znacząco wpłynąć na zmianę wartości momentów sił działających na płytę betonową, a w przypadku przekroczenia wartości dopuszczalnych dochodzi do uszkodzeń. W przypadku np. obciążeń punktowych pochodzących od regałów, przy powierzchni kontaktu nogi regału 400 cm2(stopa 20x20 cm) nacisk na beton wynosi ponad 6 MPa! Takie obciążenia wywołują duże momenty zginające w płycie. W wypadku, gdy dojdzie do przeciążenia regału lub zmiany jego położenia, to przy tak znacznych obciążeniach konieczne będzie zmniejszenie jego ciężaru, lub zmiany parametrów płyty nośnej – zwiększenie grubości płyty lub przyjęcie lepszej klasy betonu. To jednak wymaga uwzględnienia na etapie projektowania podłogi. Wzmocnienie płyty zwłaszcza w strefie kontaktu z podporami, nogami, ramami stalowymi jest jednak możliwe w sytuacji, gdy podłoga jest już wykonana i z jakiegoś powodu trzeba dokonać np. zmiany ustawień obiektów. W takim wypadku zalecane jest zastosowanie warstwy o znacząco wyższej wytrzymałości w stosunku do warstwy wierzchniej (fot.6). Opisany już wcześniej kompozyt polimerowy BELZONA®4111 pozwala na szybkie wzmocnienie powierzchni posadzki. Kompozyt BELZONA®4111 osiąga pełną wytrzymałość mechaniczną już po 24 godz. od zakończenia aplikacji i co bardzo ważne według badań przeprowadzonych w oparciu o normę ASTMC157 materiał nie wykazuje mierzalnego skurczu chemicznego podczas utwardzania
Podstawową kwestią jest to czy materiał użyty do wykonania wzmocnienia osiągnie właściwą przyczepność do betonu i czy, jak to często się dzieje, nie dojdzie do oderwania się warstwy wzmacniającej. Konieczne jest zatem sprawdzenie jakie są naprężenia w warstwie kontaktowej materiał naprawczy/płyta betonowa. Na wartość tych naprężeń mają wpływ zmienne warunki obciążenia (temperatura, wilgotność, obciążenie mechaniczne w tym skurcz).
Rozpatrzmy stan naprężenia układu Beton / kompozyt Belozna®4111. Naprężenia w kompozycie w strefie jego styku z podłożem będzie zależało od następujących czynników:
- odkształcenia betonu oraz kompozytu pod wpływem zmiennego nacisku mechanicznego
- odkształcenia betonu oraz kompozytu pod wpływem zmiennej temperatury
- skurczu utwardzania kompozytu
- nasiąkliwości kompozytu
- przyczepności kompozytu BELZONA®4111 do powierzchni betonu
- grubości warstwy
Zatem uwzględniając skurcz utwardzania oraz zmiany temperatury możemy wyznaczyć naprężenia ogólne w warstwie kompozytu, których wartość nie może przekroczyć naprężeń dopuszczalnych na rozciąganie betonu oraz wartości przyczepności warstwy kompozytu.
Dla płaskiego stanu naprężenia wprowadzając εc (odkształcenie wywołane skurczem) upraszczając wzory 1.2 ,1.3 otrzymamy :
Ponieważ wytrzymałość betonu w kierunku rozciągania (najsłabsza) przekracza często wartości naprężeń powyżej 1,6 MPa to można mieć pewność, że nałożony na jego powierzchnię kompozyt nie spowoduje zniszczenia betonu na skutek różnych rozszerzalności termicznych ani też nie oderwie się od betonu, ponieważ przyczepność kompozytu BELZONA® 4111 przekracza wartość wytrzymałości wewnętrznej betonu.
opracował: Roman Masek