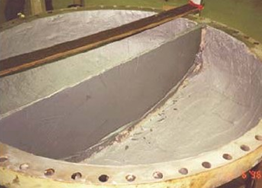
W wymiennikach ciepła, w których przynajmniej jednym z mediów uczestniczących w wymianie ciepła jest roztwór wodny, podstawowym zjawiskiem pogarszającym wydajność urządzenia jest korozja i produkty korozji powstające w wyniku jej przebiegu. Większość wymienników jest wykonana z rurek, które są szczelnie zamocowane w dnach sitowych, przy czym elementami wymienników o największej powierzchni wymiany ciepła są rurki wykonane zwykle z materiałów odpornych na korozję (stal nierdzewna lub kwasoodporna, mosiądz, miedź itp.). Pomijając bardzo cienką warstewkę pasywną tworzącą się na ich powierzchni, która zwykle stanowi niewielki opór cieplny, nic nie powoduje zakłóceń w swobodnej wy- mianie ciepła przepływającego przez ścianki rurek pomiędzy oboma mediami, gdyż rurki te nie ulegają korozji i w zasadzie są bardzo trwałe.
Problemy pojawiają się jednak w miejscu osadze- nia rurek w dnie sitowym oraz wszędzie tam, gdzie jest bezpośredni kontakt dwóch różnych materiałów (metali lub stopów), zwykle o różnych potencjałach elektrochemicznych, tj. materiału rurek i materiału den sitowych. Dwa metale lub stopy o różnych potencja- łach elektrochemicznych, połączone stykowo i zanu- rzone w roztworze wodnym stanowią elektrody ogniwa elektrochemicznego, co wywołuje przepływ ładunku elektrycznego związany z naturalnym procesem wy- równywania się potencjałów stykających się tworzyw metalowych. W zetknięciu z roztworem elektrolitu miej- sca o większej aktywności ulegają roztwarzaniu i stają się lokalnymi anodami, podczas gdy miejsca mniej aktywne elektrochemicznie przybierają rolę lokalnych katod w powstałych ogniwach galwanicznych, zwanych lokalnymi ogniwami korozyjnymi. Lokalne anody i kato- dy są krótkozwarte elektrycznie między sobą poprzez masę metalu. Energia chemiczna metali lub stopów związana z naturalnym procesem przechodzenia me- tali w tlenki, ulega zamianie na energię elektryczną tego ogniwa, co powoduje wytworzenie się ładunku elektrycznego i przepływ tego ładunku w postaci prądu elektrycznego w utworzonym obwodzie elektrycznym, zarówno w postaci jonów w roztworze wodnym, jak i elektronów w stykających się metalach.
Opisane zjawisko nosi nazwę korozji elektroche- micznej, w której procesem anodowym powodują- cym roztwarzanie się metalu lub stopu, dającym w konsekwencji ubytki masy korodującego tworzywa metalowego, jest roztwarzanie się metalu i jego prze- chodzenie do roztworu w postaci uwodnionych jonów.
Na powierzchni anody przebiegają elektrochemiczne reakcje utleniania, tj. oddawania elektronów do mate- riału elektrody przez atomy w procesie ich jonizacji, a na powierzchni katody przebiegają elektrochemiczne reakcje redukcji, tj. pobierania elektronów od materiału elektrody przez cząsteczki lub jony obecne w roztwo- rze. Anodę zawsze stanowi metal lub stop o niższym potencjale elektrochemicznym, który przechodząc do roztworu w postaci kationów oddaje elektrony przepły- wające następnie przez stykające się metale do drugiej elektrody, czyli do katody. Katodę stanowi metal o wyższym potencjale elektrochemicznym, na którym w reakcji katodowej, zwykle w reakcji redukcji tlenu, zużywane są dopływające od anody elektrony tworząc z cząsteczkami wody jony wodorotlenowe. Zjawisko to jest tym intensywniejsze (większa szybkość korozji) im większa jest różnica potencjałów pomiędzy stykający- mi się metalami lub stopami.
Zestawienie układów połączeń różnych metali sta- nowiących lokalne ogniwa korozyjne, w których lokal- ne anody ulegają korozyjnemu roztwarzaniu, stanowi praktyczne rozszerzenie szeregu napięciowego metali (tablica 1).
W przypadku stykających się ze sobą elementów ze stali węglowej z elementami miedzianymi lub z ele- mentami wykonanymi z większości wymienionych w tablicy tworzyw metalowych w środowisku wodnym to stal węglowa będzie anodą i będzie ulegała korozji (rys. 1).
W praktyce korozja elektrochemiczna dwóch róż- nych, stykających się ze sobą metali (nosi ona nazwę korozji galwanicznej) najintensywniej rozwija się w po- bliżu miejsc zetknięcia się tych metali, co szczególnie wyraźnie można zaobserwować na powierzchniach den sitowych ze zwykłej stali węglowej, w których osa- dzone są rurki metalowe z metalu lub stopu bardziej elektrododatniego. Wielkość zaatakowanej korozją powierzchni zależy od przewodnictwa elektrolitycz- nego środowiska; im przewodnictwo jest lepsze tym większa powierzchnia ulega korozji (stalowe płaszcze i przegrody komór wodnych, np. skraplacza, chłodnicy oleju itp.). W wymiennikach ciepła takich jak chłodnice oleju, skraplacze (kondensatory pary) powierzchnie anodowe stanowią: dno sitowe, przegrody w pokry- wach oraz płaszcz stalowy komory wodnej, natomiast katodę stanowią rurki wymiennika. Silna korozja dna sitowego, zwłaszcza w strefie styku z rurkami powo- duje znaczne ubytki grubości płyty dna sitowego, co może doprowadzić do utraty szczelności pomiędzy dnem i rurkami i do mieszania się mediów oraz do pogorszenia procesu wymiany ciepła. Analogiczna sytuacja zachodzi przy korozji przegród w pokrywach wymienników. Wzrost szybkości korozji elementu wymiennika ze zwykłej stali po połączeniu go z dużą liczbą rurek z tworzywa bardziej elektrododatniego o znacznie większej sumarycznej powierzchni niż ten element ulegający korozji można określić równaniem:
K = Ko ( 1 + SK/SA )
gdzie:
Ko – ubytek korozyjny stali bez kontaktu z innym metalem,
K – ubytek korozyjny stali po połączeniu elek- trycznym z metalem bardziej szlachetnym,
SA – powierzchnia korodującej stali – dno sitowe (anoda),
SK – powierzchnia tworzywa bardziej szlachet- nego – rurki (katoda),
Z powyższej zależności widać, że w przypadku gdy powierzchnia katody (rurek) jest znacznie większa od powierzchni anody (dno sitowe, przegrody) ubytek korozyjny stali K znacznie wzrasta (dno sitowe ulega przy tym silnej korozji, co uwidocznia fotografia przed- stawiona na rys. 1). Skutkom tej korozji, szczególnie w wymiennikach ciepła, w których jest duża liczba korozyjnych połączeń można zapobiegać na kilka sposobów.
Po pierwsze, można wykonać cały wymiennik cie- pła z tworzyw nierdzewnych i o takich samych poten- cjałach elektrochemicznych. Takie wymienniki są jed- nak drogie, bo wykonawstwo jest bardzo kosztowne.
Tańszym rozwiązaniem jest zastosowanie elektro- chemicznej ochrony przeciwkorozyjnej. Powszech- nym rozwiązaniem stosowanym w wymiennikach jest ochrona protektorowa, tj. montowanie elektrod wykonanych z metalu o bardziej ujemnym potencjale elektrochemicznym niż metal ulegający korozji w ko- morach wodnych, czyli montowanie protektorów. Po- wstaje przy tym ogniwo stanowiące źródło siły elektro- motorycznej potrzebnej do zahamowania pracy innych ogniw korozyjnych, w których uczestniczy powierzch- nia metalu. Przyłączona elektroda nazywana jest pro- tektorem anodowym, względnie anodą galwaniczną
c Spadek aktywności
Wzrost aktywności c |
Metale i stopy najbardziej elektroujemne – w ogniwie korozyjnym stanowią anodę
Metale najbardziej elektrododatnie –w ogniwie korozyjnym stanowią katodę |
którym jest zwykle ulegający roztwarzaniu magnez lub jego stopy, stopy aluminium, cynk i jego stopy (rys. 2 i tablica 1).
Innym sposobem ochrony powierzchni komory wodnej oraz den sitowych przed działaniem korozji jest nakładanie powłok ochronnych. Najczęściej sto- sowane są powłoki organiczne (malarskie) oraz me- talowe (powłoki natryskiwane cieplnie – metalizacja), przy czym podstawowym zagadnieniem jest jakość powłoki. Powłoka, która ma chronić narażoną na korozję powierzchnię przed kontaktem z roztworem elektrolitu (roztworem wodnym) musi być szczelna (ni- ska porowatość, brak mikropęknięć itp.) oraz powinna mieć dużą przyczepność do powierzchni metalowej. Szczelność powłoki organicznej można osiągnąć sto- sując wielokrotne malowanie (3–4-krotne), znacznie trudniejsze jest jednak osiągnięcie dobrej przyczep- ności. Przyczepność jest szczególnie istotna w strefie osadzenia rurki w dnie sitowym, a więc w miejscu, gdzie intensywność korozji jest potencjalnie najwięk- sza i gdzie brak właściwej ochrony przeciwkorozyjnej może prowadzić do przecieków mediów pomiędzy rur- ką a dnem sitowym. Przyczepność większości powłok nie przekracza 5–7 MPa.
Skutecznym sposobem zabezpieczania den si- towych przed korozją może być stosowanie powłok kompozytowych BELZONA wytwarzanych na osnowie polimerowej. Przyczepność powłoki BELZONA(1321) Ceramic S Metal do powierzchni stali jest bardzo duża i wynosi od 22 do 25 MPa. Dużą przyczepność i szczelność powłoki BELZONA(1321) na całej chronionej powierzchni, także w strefie osadzenia rurek, gwarantuje odpowiednio dokładne przygotowanie powierzchni dna sitowego metodą obróbki strumie- niowo ściernej.
Powłoka BELZONA(1321) zapewnia skuteczną ochronę podłoża stalowego dzięki wysokiej szczelności (powłoka nie zawiera części lotnych i jest bezskurczowa, co zapewnia brak mikroporów i mikro- spękań). Wśród kompozytów BELZONA, dostępne są rów- nież materiały umożliwiające odbudowę znacznych ubytków korozyjnych powstałych w wyniku wieloletniej eksploatacji wymiennika. Najczęściej stosowanym w tym celu kompozytem jest BELZONA(1111) Super Metal lub BELZONA (1311) Ceramic R Metal. Dzięki tym kompozytom można regenerować uszkodzone powierzchnie (rys. 3).
Wykorzystując technologię ochrony przeciwkorozyjnej BELZONA przeprowadzono już bardzo wiele zabiegów regeneracji starych oraz zabezpieczeń nowych wymienników ciepła, zabezpieczano dna sitowe oraz komory wodne chłodnic oleju oraz konden- satorów pary. W celu uzyskania jednakowej grubości powłok BELZONA na całej powierzchni dna sitowego konieczne jest zastosowanie odpowiednich korków (kołkowanie otworów/rurek – rys. 4), co zapewnia wy- starczającą szczelność powłok, szczególnie w strefie osadzenia rurek.
Poszczególne etapy nakładania powłok kompo- zytowych BELZONA przedstawiono na fotografiach (rys. 5 i 6).